Bending heater hoses effectively and efficiently is crucial for many automotive and industrial applications. The flexibility and durability of these hoses make them an indispensable component in cooling and heating systems. For both professionals and DIY enthusiasts, understanding the nuances of bending heater hoses can enhance the performance and longevity of their equipment.
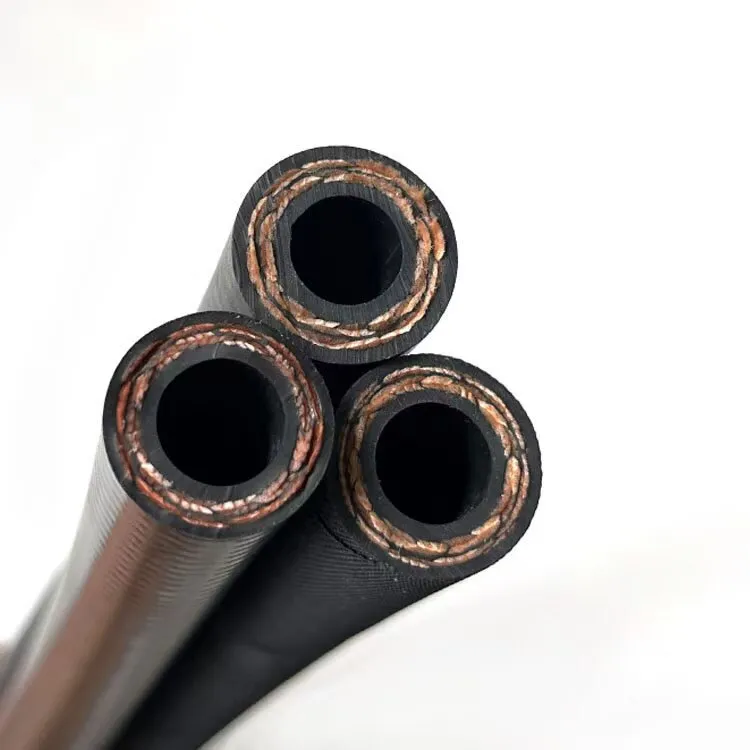
Heater hoses, typically crafted from flexible rubbers or silicone materials, are engineered for resilience and long-term performance. However, improper bending can cause kinks, which restrict the flow of fluids, or even lead to cracks, rendering them ineffective. Therefore, mastering the art of bending these hoses without compromising their integrity is essential.
Experts recommend warming the hose slightly before attempting to bend it. A gentle application of heat can increase flexibility, allowing the hose to bend more naturally without causing stress to its material. Ensure the heat is applied evenly and avoid excessive temperatures that might damage the hose.
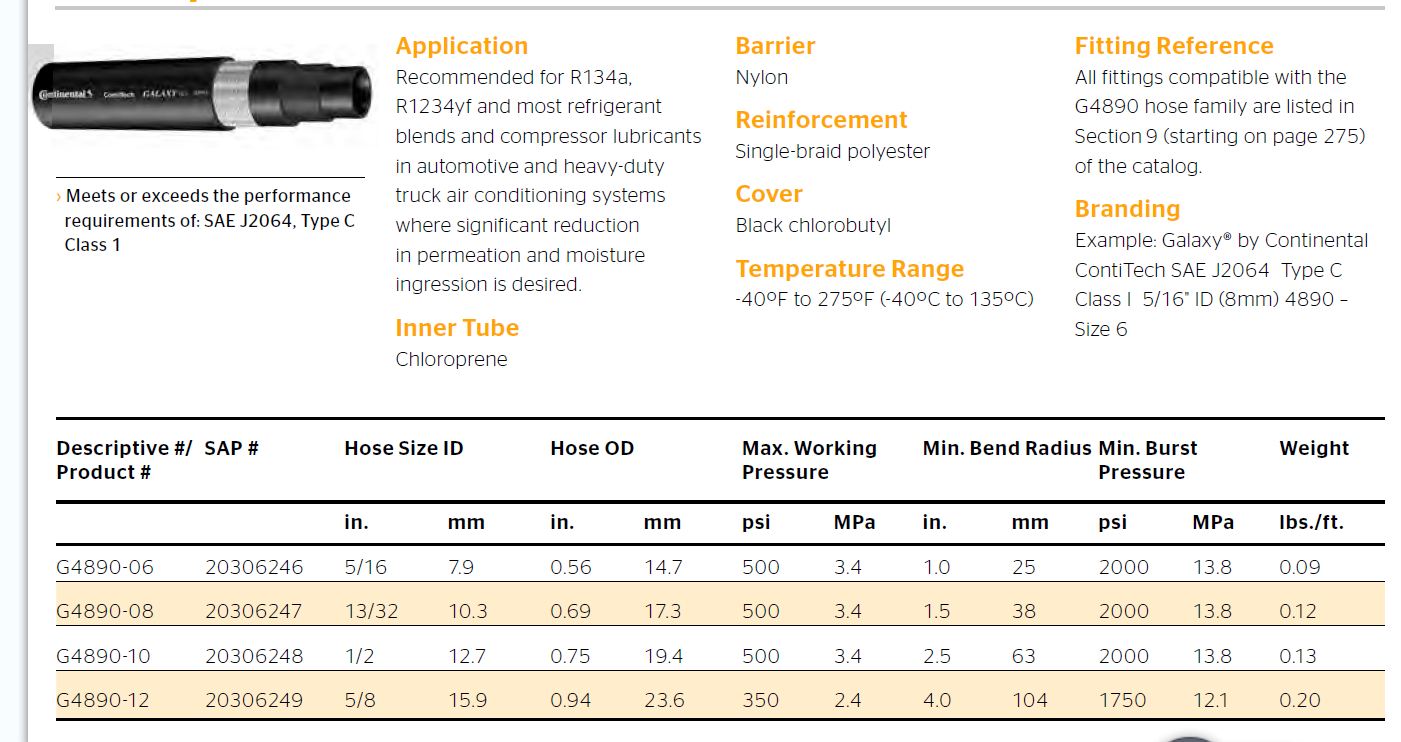
Another fundamental technique involves using a bending spring. This tool is inserted into the hose, providing internal support as you create the bend. The spring helps prevent kinking by maintaining the hose’s shape and diameter throughout the bending process. Its usage is highly recommended for tighter angles or more rigid hose materials.
For those looking to bend hoses with severe angles, coupling with elbow connectors might be advisable. These pre-formed connectors are manufactured to exact angles, ensuring there’s no compromise on the hose’s structural and functional integrity. They provide a seamless flow of fluids without the risk of potential leaks or breaks.
Adhering to the manufacturer’s specifications is paramount. Each hose has a minimum bend radius, which indicates the safest degree to which it can be bent without damage.
Exceeding this radius often results in premature wear or failure. If needing to navigate extreme bends, consider longer hose lengths or alternative routing to accommodate the hose’s limitations.
bending heater hose
Real-world experiences consistently highlight the importance of routine inspection and maintenance. Regular checks for any signs of wear, such as cracks or leaks, especially near bends, are essential for safety and functionality. Any indication of wear should prompt immediate replacement to prevent system failure.
In addressing environmental factors, consider the surroundings where the hoses will operate. Extreme temperatures, both high and low, can impact hose flexibility and durability. In colder environments, hoses are more susceptible to cracking, particularly when bent sharply. Insulation or hose covers can mitigate these risks by providing thermal protection.
Industry veteran workshops often emphasize the importance of quality when selecting heater hoses. Investing in premium-grade materials, renowned for their resistance to temperature extremes and abrasion, pays dividends in reliability and longevity. The expertise of a well-established manufacturer provides a layer of trustworthiness and authority.
Documenting these insights through professional forums and user testimonials can further solidify the authoritative voice of a brand. Sharing practical demonstrations and experiences in bending heater hoses can serve as a resourceful guide for users, fostering a community of informed consumers.
In conclusion, bending heater hoses successfully involves a blend of proper technique, quality materials, and regular maintenance. These elements ensure the operational efficiency of heating and cooling systems over time. By adhering to these expert recommendations, users can maximize the lifespan and effectiveness of their heater hoses, highlighting a commitment to excellence in mechanical applications.